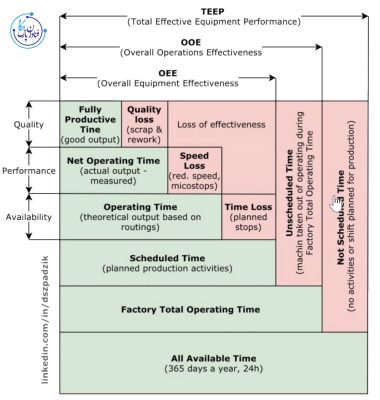
-
By روابط عمومی و بازاریابی
- In ایران بازاریابی و فروش فناوری اطلاعات
تصویر فوق یک مدل سلسله مراتبی برای ارزیابی عملکرد تولید را نشان میدهد که مبتنی بر معیارهای جهانی TEEP، OOE و OEE است. این چارچوب به سازمانها کمک میکند تا تلفات تولید را شناسایی، اندازهگیری و کاهش دهند. در این تحلیل، هر بخش به تفصیل بررسی شده است.
۱. سلسله مراتب شاخصهای کلیدی عملکرد (KPIs)
۱.۱ TEEP بهرهوری کلی تجهیزات
– تعریف: حداکثر پتانسیل تولید یک کارخانه بدون در نظر گرفتن هیچ محدودیتی.
– محاسبه:
TEEP = Availability × Performance × Quality
– دامنه اندازهگیری: تمام زمانهای ممکن (۸۷۶۰ ساعت در سال).
– کاربرد: نشان میدهد یک کارخانه چقدر میتواند از نظر تئوری به حداکثر ظرفیت خود برسد.
۱.۲ OOE بهرهوری کلی عملیات
– تعریف: عملکرد واقعی کارخانه در زمانهای عملیاتی (شامل برنامهریزی نشده).
– تفاوت با OEE: OOE زمانهای غیرفعال برنامهریزی نشده (مانند کمبود تقاضا) را نیز محاسبه میکند.
۱.۳ OEE بهرهوری کلی تجهیزات
– تعریف: استاندارد طلایی برای سنجش اثربخشی تولید در زمانهای برنامهریزی شده.
– فرمول:
OEE = Availability × Performance × Quality
– هدف: تمرکز بر کاهش ۶ تلفات بزرگ تولید (شکل ۱).
۲. اجزای اصلی OEE و تلفات مرتبط
۲.۱ دسترسی (Availability)
– محاسبه:
Availability = Operating Time / Scheduled Time
– تلفات اصلی:
– خرابی تجهیزات (Breakdowns)
– راهاندازی و تنظیمات (Setup/Adjustments)
۲.۲ عملکرد (Performance)
– محاسبه:
Performance = Net Operating Time / Operating Time
– تلفات اصلی:
– کاهش سرعت (Speed Loss)
– توقفهای جزئی (Micro-Stops)
۲.۳ کیفیت (Quality)
– محاسبه:
Quality = Fully Productive Time / Net Operating Time
– تلفات اصلی:
– ضایعات (Scrap)
– بازکاری (Rework)
۳. سطوح زمان در مدل (از کل به جزء)
| سطح زمان | توضیح | مثال تلفات |
| All Available Time | ۲۴/۷/۳۶۵ | – |
| Factory Operating Time | زمانهای واقعی فعالیت کارخانه | تعطیلات غیرمنتظره |
| Scheduled Time | زمانهای برنامهریزی شده تولید | تعمیرات برنامهریزی شده |
| Operating Time | زمان واقعی کار ماشینآلات | خرابیها |
| Net Operating Time | زمان تولید موثر | کاهش سرعت |
| Fully Productive Time | زمان تولید محصولات سالم | ضایعات |
۴. کاربرد عملی مدل
۴.۱ تحلیل تلفات
– مثال: اگر OEE یک دستگاه ۶۰٪ باشد، میتوان با بررسی سهم هر جزء (مثلاً Availability=70%، Performance=85%، Quality=90%)، دقیقاً تشخیص داد که بزرگترین منبع تلفات کجاست.
۴.۲ بهبود مستمر
– راهکارها:
– افزایش Availability: اجرای نگهداری پیشگیرانه (TPM).
– بهبود Performance: بهینهسازی تنظیمات ماشینآلات.
– ارتقای Quality: آموزش اپراتورها و کنترل کیفیت بلادرنگ.
۴.۳ مقایسه استانداردها
– معیارهای صنعتی:
– OEE عالی: >85%
– OEE متوسط: 60-70%
– OEE ضعیف: <40%
۵. محدودیتها و ملاحظات
– چالشها:
– نیاز به جمعآوری دقیق دادههای تولید.
– عدم توجه به عوامل انسانی در برخی پیادهسازیها.
– راهکار: تلفیق با روشهایی مانند Lean Manufacturing.
نتیجهگیری که از این عکس مهم میشه گرفت :
این چارچوب یک نقشه راه سیستماتیک برای شناسایی “پنجرههای شکسته” تولید ارائه میدهد.
با تمرکز بر TEEP به عنوان هدف نهایی، سازمانها میتوانند با بهبود گامبهگام OEE و OOE، به بهرهوری حداکثری دست یابند.
موفقیت در اجرا نیازمند یکپارچهسازی این معیارها با استراتژیهای عملیاتی و فرهنگ سازمانی است.
اینجاست که باید گفت : فرهنگ سازمانی چقدر مهم است .
شکل ۱: ۶ تلفات بزرگ تولید در مدل OEE
۱) خرابیها، (۲) تنظیمات، (۳) توقفهای کوچک، (۴) کاهش سرعت، (۵) ضایعات، (۶) بازکاری